What Size Staples Should You Use for Roofing Felt?
When it comes to roofing projects, ensuring that your materials are secured properly is crucial for both durability and performance. One of the key components often overlooked is the type and size of staples used for roofing felt. While it may seem like a minor detail, choosing the right staples can make a significant difference in the longevity of your roofing system. In this article, we will explore the various factors that influence staple selection, helping you make informed decisions for your next roofing endeavor.
Roofing felt serves as a protective barrier between your roof deck and the shingles, providing an essential layer of moisture resistance. To effectively secure this material, it’s important to understand the specifications of staples that are best suited for the job. Factors such as the thickness of the felt, the type of roofing system, and local building codes can all play a role in determining the appropriate staple size.
In addition to size, the material and design of the staples themselves can impact their performance under various weather conditions. Whether you are a seasoned contractor or a DIY enthusiast, knowing the right staples to use will not only enhance the integrity of your roofing project but also save you time and resources in the long run. Join us as we delve deeper into the specifics of selecting the ideal staples for roofing felt and ensure your roofing project stands
Choosing the Right Size Staples
When selecting staples for roofing felt, it’s essential to consider both the size and type of staples that will provide optimal performance in terms of holding power and durability. The most common staples used in roofing applications are pneumatic staples, which are driven into the material using an air-powered staple gun.
The typical size for staples used in roofing felt is:
- Length: 1 inch to 1.5 inches
- Width: 1/4 inch to 3/8 inch crown width
Using staples of the appropriate length ensures that they penetrate the roofing felt and securely anchor into the underlying substrate, which is often plywood or oriented strand board (OSB).
Types of Staples
Different types of staples can be used based on the roofing felt material and the specific project requirements:
- Galvanized Staples: These are rust-resistant and ideal for outdoor use, especially in areas where moisture is a concern.
- Stainless Steel Staples: While more expensive, they offer superior corrosion resistance and are suitable for coastal areas with high salinity.
- Plastic-Coated Staples: These provide additional weather resistance and can be useful in certain climates.
Staple Application Techniques
Proper application techniques are crucial for ensuring that roofing felt is secured effectively. Here are some guidelines:
- Spacing: Staples should be placed approximately every 6 to 8 inches along the edges of the roofing felt and every 12 to 18 inches in the field (center area) of the felt.
- Angle: Staples should be applied perpendicular to the surface of the felt to maximize holding power.
- Depth: Ensure that the staples are driven flush with the surface of the felt without overdriving, which could damage the material.
Staple Size | Use Case | Material |
---|---|---|
1 inch | Lightweight felt applications | Galvanized or stainless steel |
1.5 inches | Heavy-duty felt applications | Galvanized or stainless steel |
1 inch | Plastic roofing felt | Plastic-coated or galvanized |
Selecting the right size and type of staples, as well as employing proper application techniques, will significantly enhance the integrity and lifespan of the roofing felt, ensuring it performs effectively under various weather conditions.
Recommended Staple Size for Roofing Felt
When installing roofing felt, the choice of staple size is crucial for ensuring a secure and durable application. The recommended staple size typically varies depending on the type of roofing felt and the specific roofing system in use. Here are some guidelines to help you select the appropriate staple size:
- Length: Use staples that are at least 1 inch to 1.5 inches long. This length is sufficient to penetrate through the felt and into the underlying decking or substrate.
- Gauge: Opt for staples that are made of 16-gauge or 18-gauge wire. Thicker gauge staples provide better holding power and resistance to weather elements.
Staple Placement Guidelines
Proper placement of staples is essential to ensure the roofing felt stays in position over time. Follow these guidelines for effective staple placement:
- Place staples every 12 to 18 inches along the edges of the felt.
- Staple the felt down at least every 24 inches in the field area (the main body of the felt away from the edges).
- Ensure staples are driven flush with the surface of the felt to avoid puncturing the material or creating lumps.
Types of Staples for Roofing Felt
Various types of staples are suitable for roofing felt, each offering different benefits. Below is a comparison of common staple types:
Type of Staple | Material | Advantages |
---|---|---|
Galvanized Staples | Galvanized Steel | Corrosion-resistant; ideal for outdoor use. |
Stainless Steel Staples | Stainless Steel | Highly resistant to rust and corrosion; best for coastal areas. |
Plastic Coated Staples | Steel with Plastic Coating | Offers some corrosion resistance; easy to handle and apply. |
Considerations for Different Roofing Systems
The roofing system in use may influence staple selection and application. Here are some considerations based on common types of roofing systems:
- Asphalt Shingles: Use 1-inch galvanized staples to secure felt underlayment.
- Metal Roofing: Stainless steel staples are recommended to prevent rusting and maintain integrity.
- Tile Roofing: Opt for longer staples (1.5 inches) to accommodate thicker felt and ensure secure attachment.
Tools for Stapling Roofing Felt
Utilizing the right tools will enhance the efficiency of installing roofing felt. Recommended tools include:
- Heavy-Duty Stapler: A pneumatic or electric stapler can speed up the installation process and improve staple penetration.
- Handheld Stapler: For smaller projects, a manual stapler can be effective, though it may require more effort.
- Staple Gun with Adjustable Settings: Allows for varying staple lengths and depths based on specific felt thickness.
Expert Recommendations on Staple Sizes for Roofing Felt
James Carter (Roofing Specialist, National Roofing Contractors Association). “For roofing felt installation, a staple size of 1 inch is typically recommended. This length provides adequate penetration into the roof deck, ensuring a secure hold while minimizing the risk of tearing the felt during installation.”
Linda Martinez (Construction Materials Engineer, Building Science Institute). “Using 1/2 inch to 3/4 inch staples is generally sufficient for roofing felt applications. These sizes allow for a balance between holding power and ease of installation, particularly when working with lighter felt products.”
Robert Chen (Building Code Consultant, International Code Council). “When selecting staple sizes for roofing felt, it is crucial to consider the local building codes. Most codes specify a minimum staple length of 3/4 inch to ensure compliance with wind resistance requirements.”
Frequently Asked Questions (FAQs)
What size staples are recommended for roofing felt?
The recommended staple size for roofing felt is typically 1-inch to 1.5-inch long staples. This length ensures adequate penetration into the underlying material for secure attachment.
Can I use regular office staples for roofing felt?
Regular office staples are not suitable for roofing felt due to their insufficient length and strength. Roofing applications require heavy-duty staples designed to withstand outdoor conditions.
What type of stapler should I use for roofing felt?
A pneumatic or manual staple gun specifically designed for heavy-duty applications is ideal for roofing felt. These tools provide the necessary power to drive staples securely into the roofing material.
How far apart should staples be placed when installing roofing felt?
Staples should be placed approximately 12 inches apart along the edges and every 18 inches in the field of the felt. This spacing ensures proper adhesion and minimizes the risk of wind uplift.
Are there any specific conditions that affect staple choice for roofing felt?
Yes, environmental conditions such as wind exposure and moisture levels can affect staple choice. In high-wind areas, longer and heavier-duty staples may be necessary to ensure stability.
Is it necessary to use a specific type of staple for different roofing felt materials?
While the staple size remains consistent, the type of staple may vary based on the roofing felt material. For example, thicker felt may require heavier gauge staples for optimal performance.
In summary, selecting the appropriate size staples for roofing felt is crucial for ensuring a secure and durable installation. The commonly recommended staple size for roofing felt is typically 1-inch to 1.5-inch long staples, which provide adequate penetration into the underlying materials while maintaining a strong hold. It is essential to choose staples that are corrosion-resistant, particularly when working with roofing materials exposed to the elements.
Additionally, the spacing of the staples plays a significant role in the effectiveness of the roofing felt installation. Staples should be placed approximately 8 to 12 inches apart along the edges and seams of the felt to prevent wind uplift and water intrusion. Proper installation techniques, including the use of the correct staple size and spacing, contribute to the longevity and performance of the roofing system.
Ultimately, understanding the specifications for staple size and application is vital for both professional roofers and DIY enthusiasts. By adhering to these guidelines, individuals can ensure that their roofing felt is installed correctly, providing a reliable barrier against moisture and enhancing the overall integrity of the roofing structure.
Author Profile
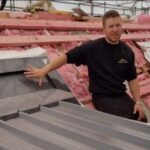
-
Hi, I’m Victor - the voice behind Element Roofing.
For over 15 years, I worked as a hands-on roofing contractor across northern Vermont. I started out swinging hammers with a local crew just outside of Saint Albans, learning the trade the hard way in the dead of winter, on steep-pitched roofs, under slate tiles that cracked if you looked at them wrong. Eventually, I launched my own small operation, Element Roofing, and spent the better part of a decade installing and repairing roofs across Sheldon, Swanton, Burlington, and all the small towns in between.
But people wanted to understand what was happening over their heads. They asked smart questions. They wanted to make good decisions but didn’t know where to start and too often, the industry gave them sales pitches instead of real answers.
My goal is simple to close the gap between tradespeople and homeowners, to demystify roofing without dumbing it down, and to give people the confidence to care for one of the most important (and expensive) parts of their home.
So feel free to dig in, explore, and take control of what’s over your head. We’re here to help from rafter to ridge.
Latest entries
- May 6, 2025Roof MaintenanceIs a Roof Leak Really Considered an Emergency? What You Need to Know!
- May 6, 2025Roof MaintenanceDoes the Seahawks Stadium Feature a Retractable Roof?
- May 6, 2025Roof MaterialsDo Owens Corning Duration Shingles Qualify for a Tax Credit?
- May 6, 2025Roof MaterialsDo You Really Need Starter Shingles for Your Roof?