How Do You Build a Flat Roof: A Step-by-Step Guide for Beginners?
Building a flat roof can be an exciting yet daunting project for homeowners and builders alike. Unlike traditional pitched roofs, flat roofs offer a unique aesthetic and functional appeal, making them a popular choice for modern architecture and urban settings. Whether you’re looking to create a rooftop garden, install solar panels, or simply enjoy the sleek lines of a contemporary design, understanding the nuances of flat roof construction is essential. In this article, we will guide you through the key considerations, materials, and techniques needed to successfully build a flat roof that stands the test of time.
When embarking on the journey of constructing a flat roof, it’s crucial to grasp the fundamental principles that differentiate it from other roofing styles. Flat roofs require careful planning to ensure proper drainage, structural integrity, and insulation. The choice of materials—ranging from traditional tar and gravel to modern single-ply membranes—can significantly impact both the longevity and performance of the roof. Additionally, understanding local building codes and weather conditions is vital to creating a roof that not only looks good but also functions effectively in your specific environment.
Moreover, the construction process itself involves several stages, from framing and sheathing to waterproofing and finishing touches. Each step plays a critical role in the overall durability and usability of the roof space.
Materials Needed for Building a Flat Roof
When constructing a flat roof, the selection of materials is critical to ensure durability and performance. The following materials are commonly used:
- Roof Decking: Typically made from plywood or oriented strand board (OSB), it forms the base of the roof.
- Insulation: Rigid foam boards or spray foam insulation are recommended to enhance energy efficiency.
- Waterproof Membrane: Options include EPDM rubber, TPO, or PVC membranes that provide a waterproof barrier.
- Flashing: Metal flashing is essential to protect joints and transitions from water intrusion.
- Drainage System: Gutters and downspouts, or internal drains, help manage water runoff.
- Roof Coating: Reflective coatings can be applied to extend the life of the membrane and improve energy efficiency.
Steps to Build a Flat Roof
Building a flat roof involves several systematic steps, ensuring safety and compliance with building codes. Below is a detailed process:
- Design the Roof Structure: Determine the roof pitch, drainage, and overall design according to local regulations.
- Prepare the Site: Clear the area of debris, and ensure the existing structure can support the new roof.
- Install the Roof Deck: Lay down plywood or OSB boards, securing them with nails or screws, ensuring a tight fit.
- Add Insulation: Place rigid foam boards on top of the decking to improve thermal resistance, ensuring they fit snugly.
- Apply Waterproof Membrane: Roll out the chosen membrane, ensuring overlaps are adequately sealed. Use adhesives or fasteners as recommended by the manufacturer.
- Install Flashing: Apply metal flashing around edges, vents, and any other protrusions to prevent water infiltration.
- Set Up Drainage: Ensure proper drainage by installing gutters, downspouts, or internal drains as per the design.
- Finish with Roof Coating: Apply a reflective roof coating to protect the membrane and enhance energy efficiency.
Considerations for Flat Roof Construction
When constructing a flat roof, several factors must be considered to ensure long-lasting performance:
- Water Drainage: Flat roofs must have a slight slope (minimum of 1-2%) to facilitate drainage.
- Load-Bearing Capacity: Ensure the structure can support the roof’s weight, including potential snow loads.
- Local Climate: Choose materials and designs suitable for the local weather conditions.
- Building Codes: Adhere to local building codes and regulations for flat roof construction.
Material | Advantages | Disadvantages |
---|---|---|
EPDM Rubber | Durable, cost-effective, UV resistant | Can be punctured; requires proper installation |
TPO | Energy-efficient, lightweight, easy to install | Less durable than EPDM; may shrink over time |
PVC | Highly durable, excellent for drainage | Higher initial cost; requires skilled installation |
By carefully considering materials, following a structured construction process, and addressing specific considerations, a flat roof can be effectively built to meet both functional and aesthetic requirements.
Understanding Flat Roof Types
Flat roofs come in various types, each with distinct characteristics and installation methods. Selecting the appropriate type is crucial for ensuring durability and functionality.
- Built-Up Roofing (BUR): Composed of multiple layers of roofing felt and asphalt, BUR provides excellent waterproofing and is suitable for low-slope applications.
- Modified Bitumen: This type combines traditional BUR with modern materials, offering flexibility and ease of installation. It is often applied in sheets using heat or adhesive.
- EPDM (Ethylene Propylene Diene Monomer): A rubber membrane that is highly resistant to UV rays and weathering, EPDM is known for its longevity and ease of repair.
- TPO (Thermoplastic Olefin): This single-ply roofing membrane is energy-efficient and reflects UV rays, making it a popular choice for commercial buildings.
- PVC (Polyvinyl Chloride): PVC roofs are durable and energy-efficient, offering resistance to chemicals and fire, ideal for industrial applications.
Essential Materials and Tools
To construct a flat roof effectively, a variety of materials and tools are needed. Below is a comprehensive list.
Materials:
- Roofing Membrane: Choose between BUR, modified bitumen, EPDM, TPO, or PVC based on specific needs.
- Insulation Boards: Provide thermal resistance and support.
- Adhesive: Depending on the membrane type, select the appropriate adhesive for bonding.
- Flashing: Use metal or rubber flashing to prevent water intrusion at seams and edges.
- Drainage Components: Include scuppers, gutters, or internal drains to manage water runoff.
Tools:
- Utility Knife: For cutting roofing material.
- Rollers: Essential for applying adhesive and ensuring proper bonding.
- Ladder: For accessing the roof safely.
- Safety Gear: Helmets, gloves, and harnesses to maintain safety during installation.
- Measuring Tape: For accurate measurements of roofing materials.
Installation Steps
Following a structured approach during installation ensures the flat roof’s effectiveness and longevity.
- Preparation:
- Inspect the existing roof structure for damage and ensure proper drainage.
- Remove any old roofing material and debris.
- Install Insulation:
- Lay down insulation boards over the roof deck, ensuring a tight fit.
- Adhere the boards using the appropriate adhesive.
- Apply the Roofing Membrane:
- Roll out the selected membrane and cut it to size.
- Secure the membrane using adhesive or mechanical fasteners, following the manufacturer’s guidelines.
- Seal Joints and Edges:
- Use flashing to seal all joints, ensuring no water can infiltrate.
- Pay special attention to areas around vents and chimneys.
- Install Drainage Solutions:
- Incorporate scuppers or gutters to facilitate water drainage.
- Test drainage by running water over the roof.
- Final Inspection:
- Conduct a thorough inspection to ensure the roof is watertight and that all seams and edges are properly sealed.
Maintenance Tips for Flat Roofs
Regular maintenance is essential for extending the lifespan of a flat roof. Consider the following practices:
- Routine Inspections: Perform inspections at least twice a year and after severe weather events.
- Clear Debris: Remove leaves, branches, and other debris that may accumulate on the roof.
- Check for Leaks: Look for signs of water pooling or leaks, particularly around seams and flashing.
- Maintain Drainage Systems: Ensure gutters and drains are clear of blockages to prevent water buildup.
- Repair Promptly: Address any damage or wear immediately to prevent further issues.
By adhering to these guidelines, you can effectively construct and maintain a flat roof, ensuring its performance and durability for years to come.
Expert Insights on Building a Flat Roof
“Building a flat roof requires careful consideration of drainage. Properly sloped surfaces are essential to prevent water pooling, which can lead to leaks and structural damage over time. Utilizing high-quality waterproofing materials is also crucial for longevity.”
“Incorporating insulation into a flat roof design not only enhances energy efficiency but also contributes to the overall durability of the structure. A well-insulated flat roof can significantly reduce heating and cooling costs.”
“When selecting materials for a flat roof, consider the local climate and environmental conditions. For instance, in areas with heavy snowfall, a reinforced membrane may be necessary to withstand the added weight and prevent collapse.”
Frequently Asked Questions (FAQs)
What materials are commonly used to build a flat roof?
Common materials for flat roofs include EPDM rubber, TPO (thermoplastic polyolefin), PVC (polyvinyl chloride), modified bitumen, and built-up roofing (BUR) systems. Each material offers different benefits in terms of durability, cost, and insulation properties.
How do I ensure proper drainage on a flat roof?
To ensure proper drainage, incorporate a slight slope in the roof design, typically a minimum of 1-2%. Install drains or scuppers at low points to facilitate water runoff and prevent ponding, which can lead to leaks and structural damage.
What is the best insulation for a flat roof?
The best insulation options for flat roofs include rigid foam board insulation, spray foam insulation, and fiberglass batts. Rigid foam boards are often preferred due to their high R-value and moisture resistance.
How often should I inspect and maintain a flat roof?
Regular inspections should occur at least twice a year, ideally in spring and fall. Additionally, inspect after severe weather events. Routine maintenance includes clearing debris, checking for leaks, and ensuring drainage systems are functioning properly.
Can I install a flat roof myself, or should I hire a professional?
While some homeowners may successfully install a flat roof themselves, it is generally recommended to hire a professional. Proper installation requires specific skills and knowledge to ensure durability, waterproofing, and compliance with building codes.
What are the common problems associated with flat roofs?
Common problems include water pooling, leaks, membrane damage, and poor drainage. Regular maintenance and prompt repairs are essential to mitigate these issues and extend the roof’s lifespan.
Building a flat roof involves several critical steps that ensure durability, functionality, and aesthetic appeal. First, it is essential to choose the right materials, such as EPDM, TPO, or modified bitumen, which are known for their waterproofing capabilities and longevity. Proper insulation is also crucial to enhance energy efficiency and prevent heat loss. Additionally, the design must include a slight slope to facilitate water drainage, preventing potential pooling that could lead to leaks and structural damage.
Preparation and planning play a significant role in the construction process. This includes assessing the existing structure, obtaining necessary permits, and ensuring compliance with local building codes. Furthermore, safety measures should be prioritized throughout the construction phase, including the use of appropriate personal protective equipment and adherence to safety protocols. Engaging professionals or experienced contractors can also help mitigate risks and ensure that the project meets quality standards.
building a flat roof is a multifaceted endeavor that requires careful consideration of materials, design, and safety. By following best practices and focusing on quality workmanship, homeowners and builders can create a flat roof that not only enhances the aesthetic of the property but also provides long-lasting protection against the elements. Ultimately, investing time and resources into the planning and execution of a flat roof
Author Profile
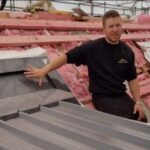
-
Hi, I’m Victor - the voice behind Element Roofing.
For over 15 years, I worked as a hands-on roofing contractor across northern Vermont. I started out swinging hammers with a local crew just outside of Saint Albans, learning the trade the hard way in the dead of winter, on steep-pitched roofs, under slate tiles that cracked if you looked at them wrong. Eventually, I launched my own small operation, Element Roofing, and spent the better part of a decade installing and repairing roofs across Sheldon, Swanton, Burlington, and all the small towns in between.
But people wanted to understand what was happening over their heads. They asked smart questions. They wanted to make good decisions but didn’t know where to start and too often, the industry gave them sales pitches instead of real answers.
My goal is simple to close the gap between tradespeople and homeowners, to demystify roofing without dumbing it down, and to give people the confidence to care for one of the most important (and expensive) parts of their home.
So feel free to dig in, explore, and take control of what’s over your head. We’re here to help from rafter to ridge.
Latest entries
- May 6, 2025Roof MaintenanceIs a Roof Leak Really Considered an Emergency? What You Need to Know!
- May 6, 2025Roof MaintenanceDoes the Seahawks Stadium Feature a Retractable Roof?
- May 6, 2025Roof MaterialsDo Owens Corning Duration Shingles Qualify for a Tax Credit?
- May 6, 2025Roof MaterialsDo You Really Need Starter Shingles for Your Roof?